News & Articles
Welcome to the Mascot Power Blog where you will find news and articles about Power Supplies and Battery Chargers.


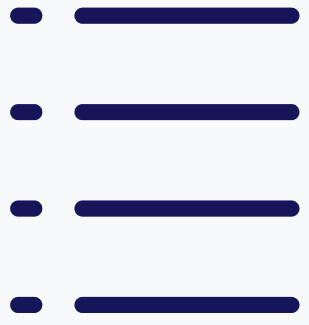
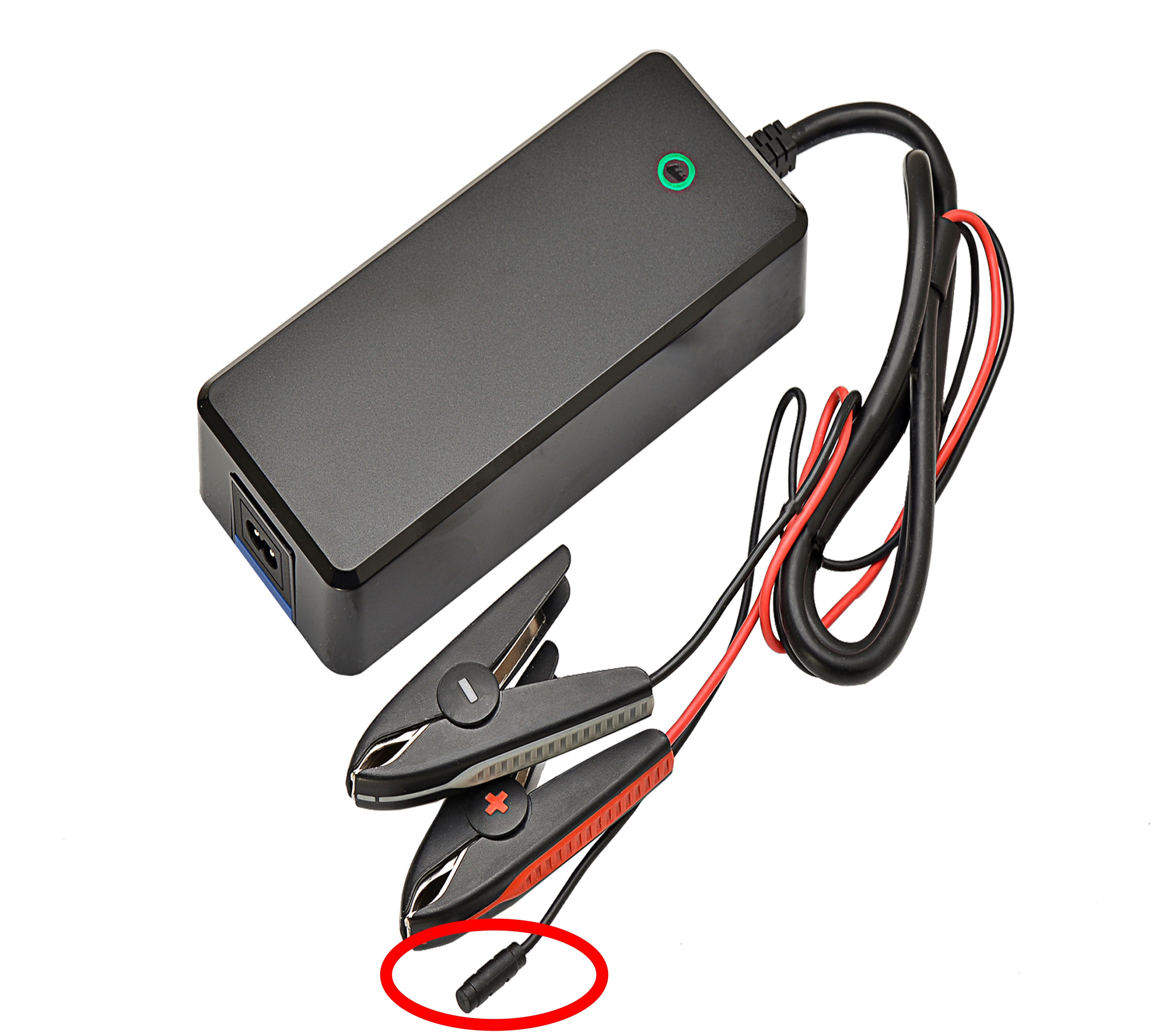
Understanding Temperature Derating in Power Supplies
Ambient temperature has a direct effect on the performance and longevity of power supplies and battery chargers.
Read more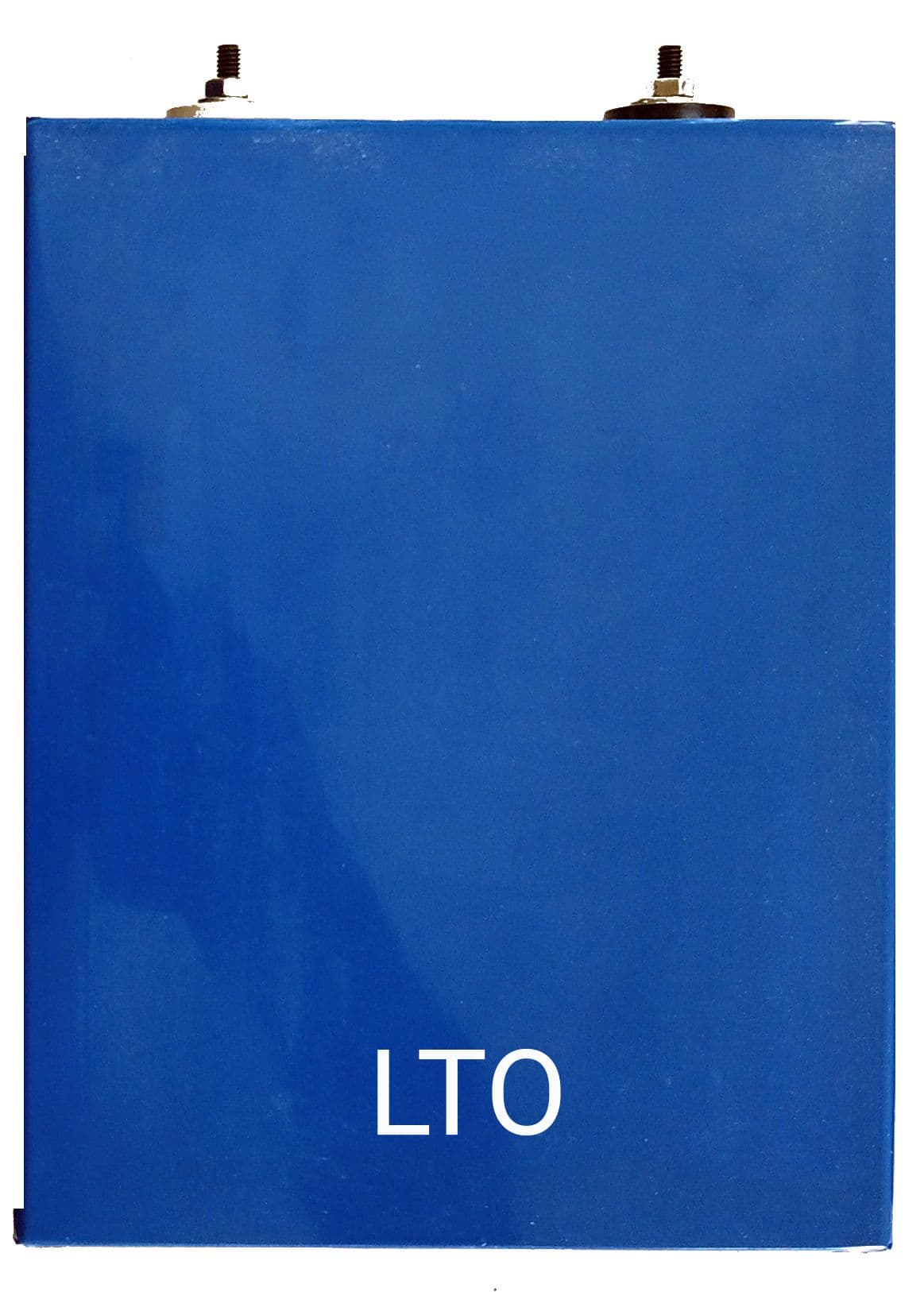
Charging Lithium Titanate Oxide (LTO) batteries
Lithium Titanate Oxide (LTO) batteries are gaining traction across industries that require rapid charging, wide temperature operation, and extended cycle life.
Read more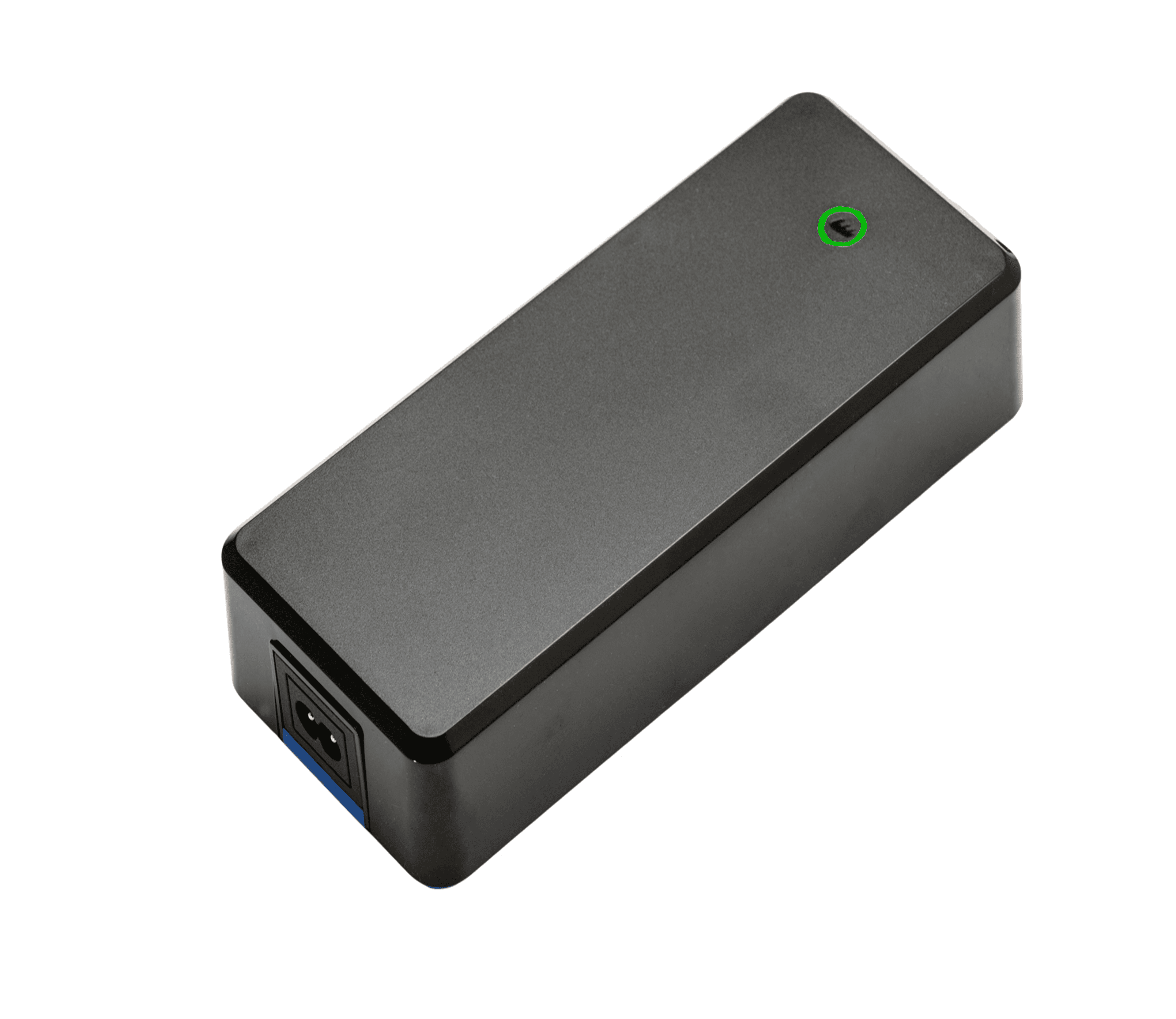
New model 4340 Battery Charger (max. 80W)
Engineered for maximum performance and reliability, the 4340 employs a microcontroller-managed 3-stage charging profile, optimizing battery life and runtime.
Read more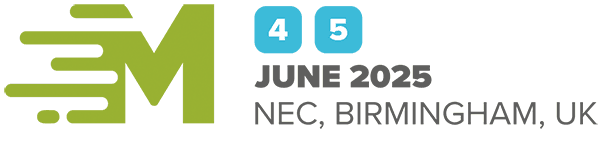
We’ll be exhibiting at Med-Tech Innovation Expo in Birmingham on 4–5 June!
We’ll be exhibiting at Med-Tech Innovation Expo in Birmingham on 4–5 June. Visit us at Hall 2, Stand J3 to learn more about our certified power supply and charging solutions for medical devices
Read more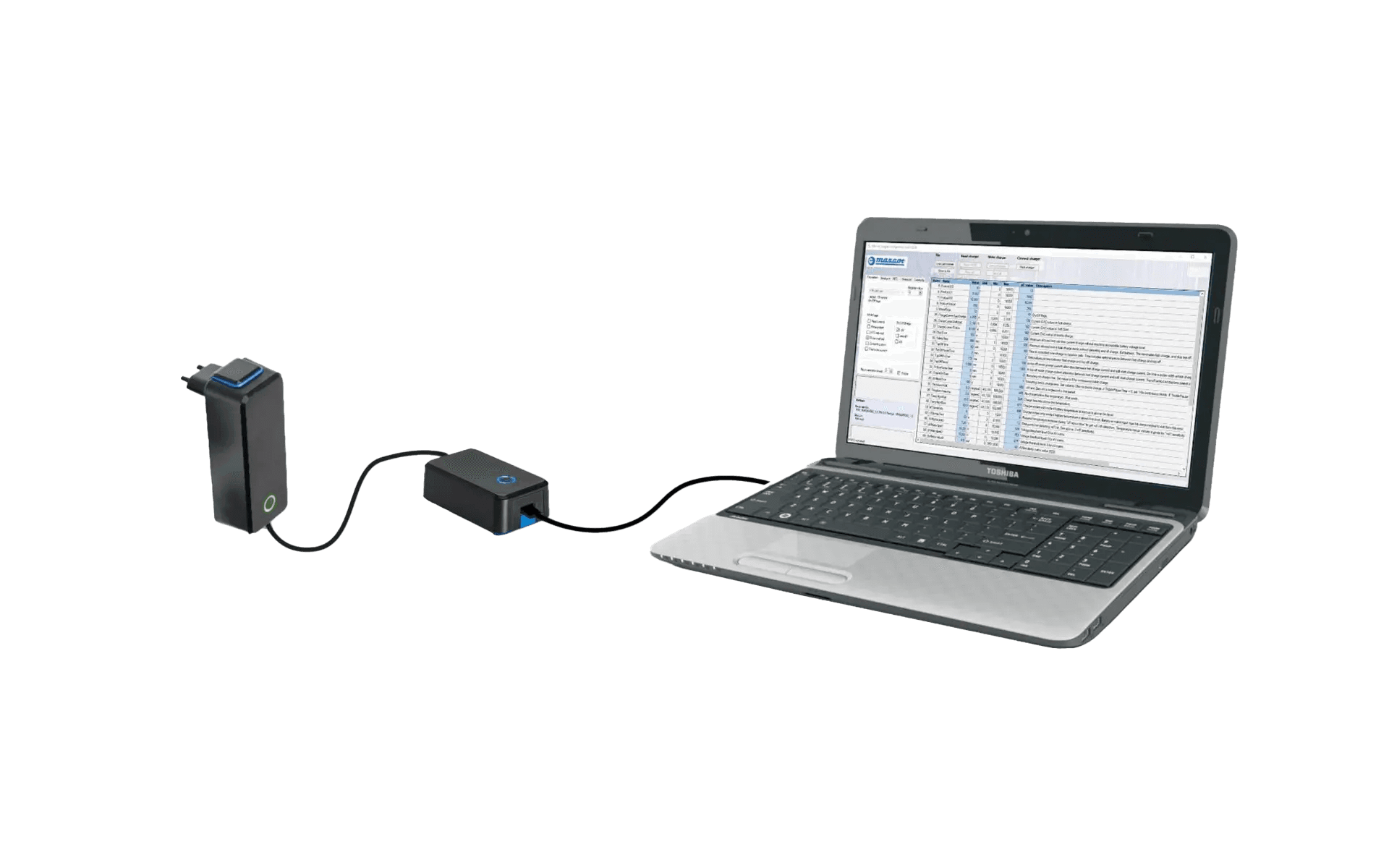
CBC (configurable battery charger) programming module for LiFePO4 batteries
Our latest blog explores our CBC module and config software for lithium iron phosphate (LiFePO4) battery charging.
Read more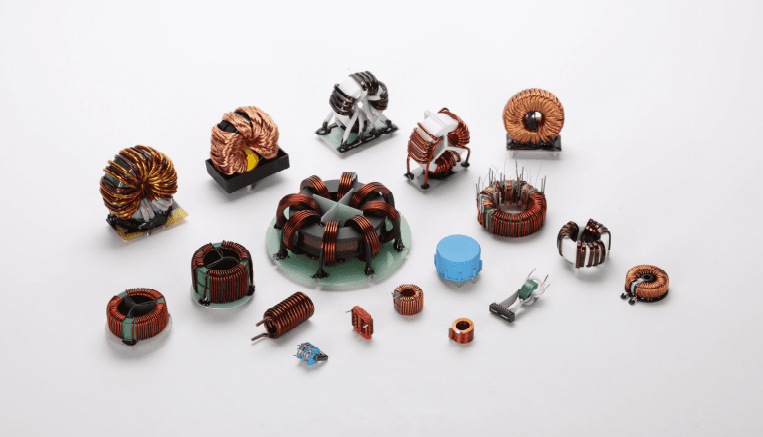
What to Consider When Choosing a Supplier for Custom Inductive Components
Mascot Ningbo offers customisable Transformers and Chokes to meet specific requirements
Read more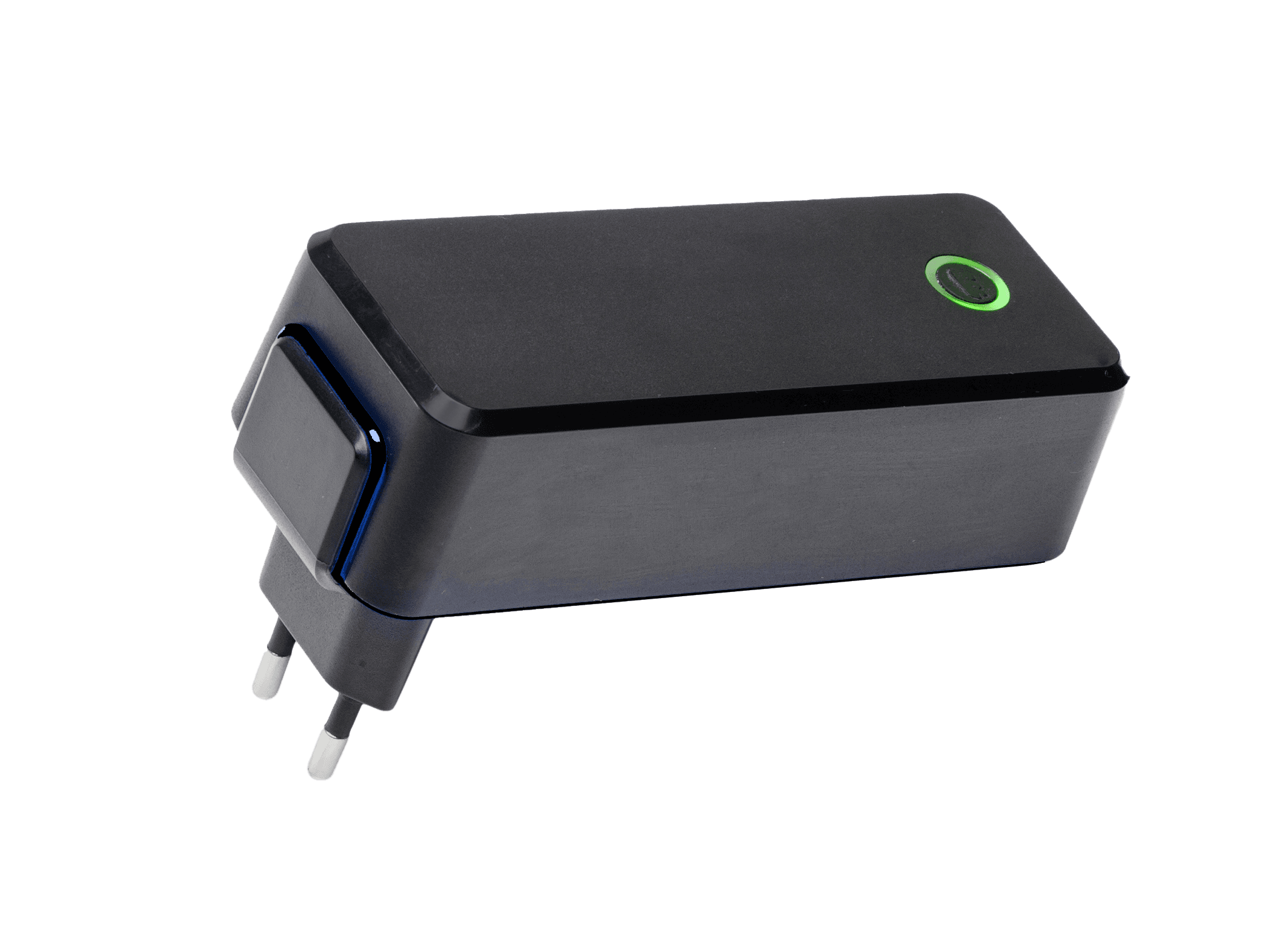
New model 4440 Battery Charger (max. 2A)
The new model 4440 battery charger (max. 2A) is designed for cost-conscious applications that don't require special certifications
Read more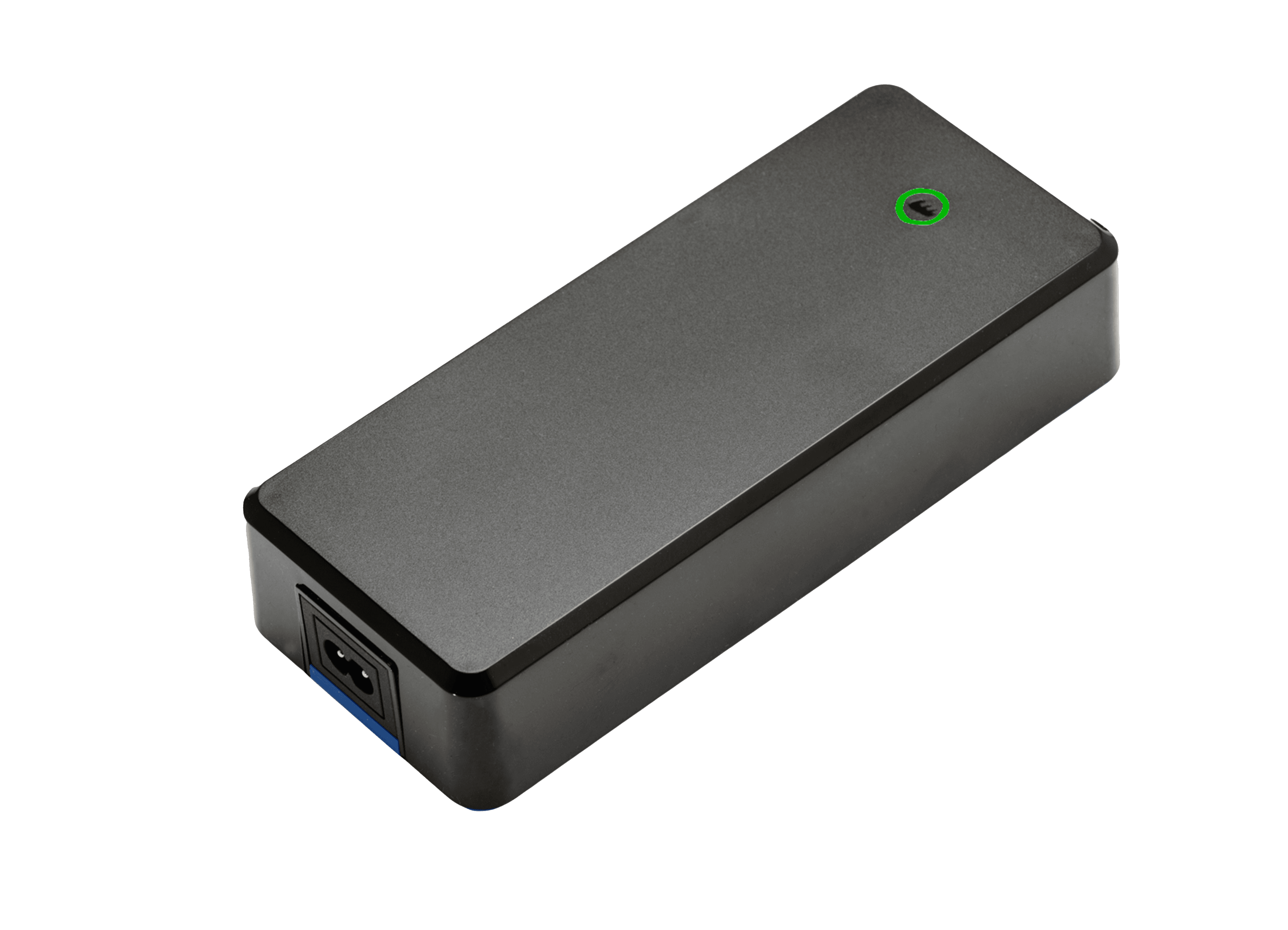
Adding LiFe to the model 4040 family!
Max output power 8A, charging 4 to 16 LiFePO4 battery cells.
Read more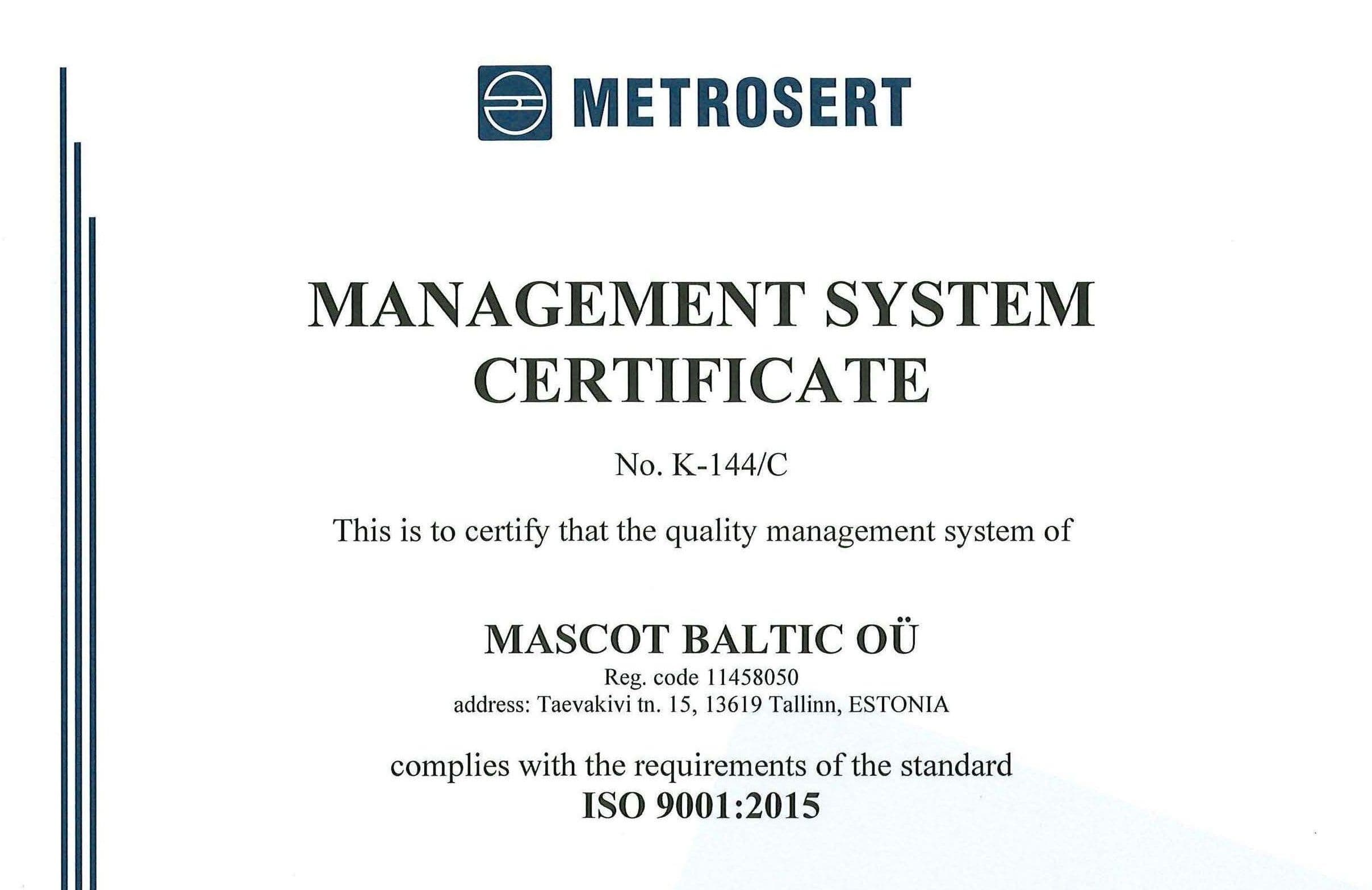
Mascot Baltic Renew ISO-9001 Certificate
Mascot Baltic successfully passed 3-year recertification ISO-9001 audit.
Read more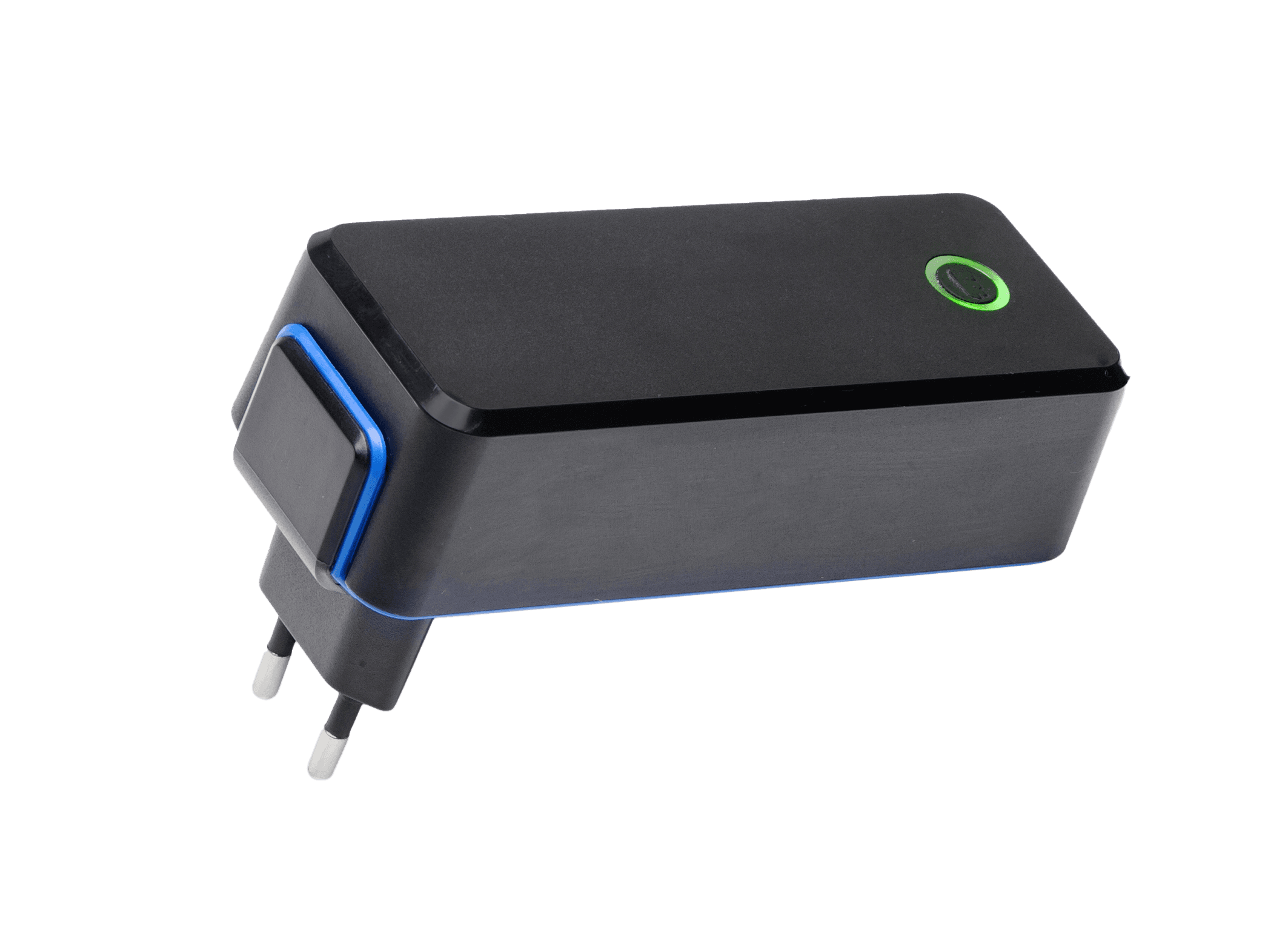
Model 3546 is now available for charging LiFePO4 batteries
The first versions are designed for 4-cell and 8-cell LiFePO4 battery packs.
Read more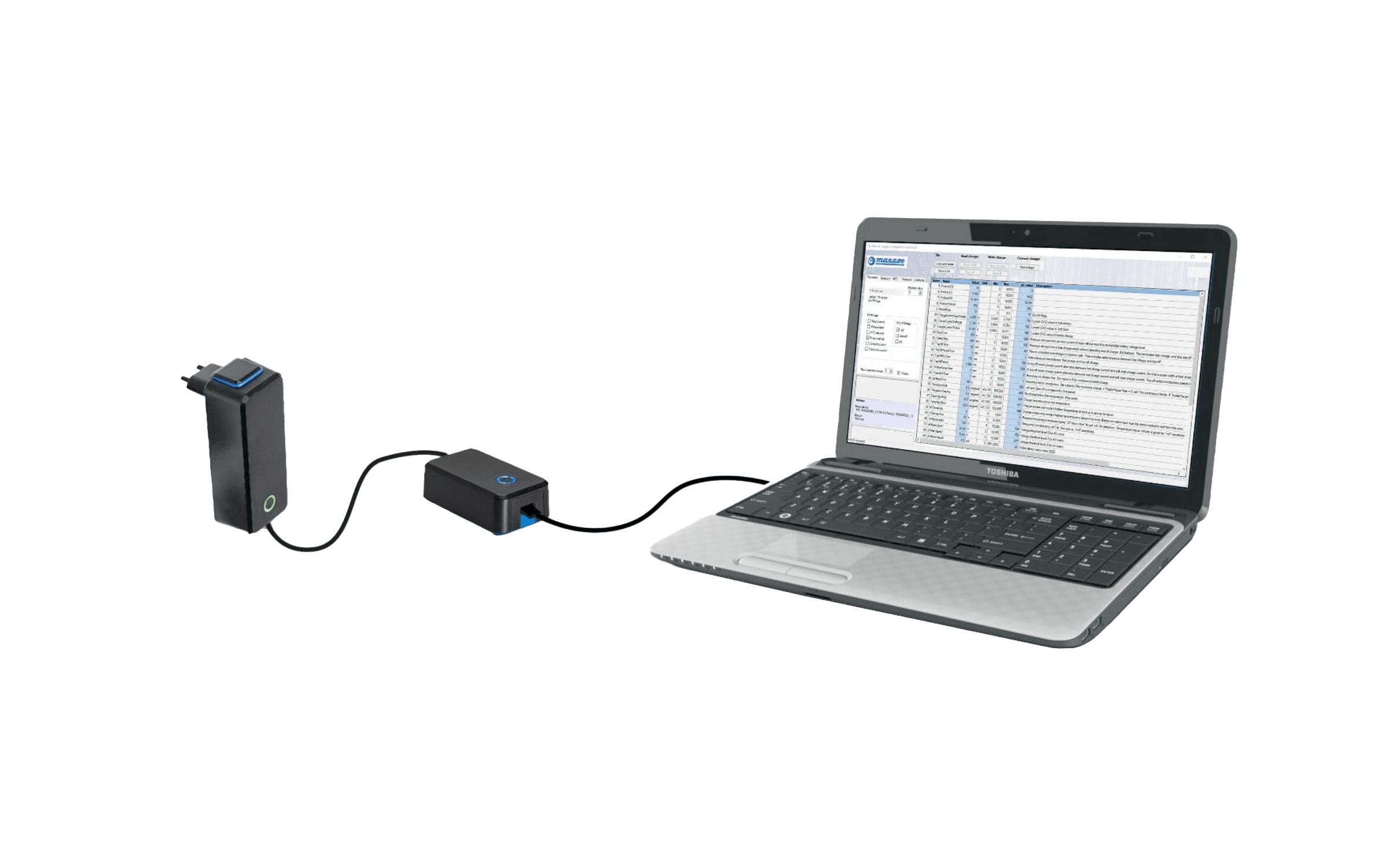
CBC (configurable battery charger) programming module for LiFePO4 batteries
Configurable battery chargers offer users the flexibility to adjust charging parameters for increased optimisation and compatibility. Every Mascot CBC is ready for immediate use without the need for configuration. However, they can also be optimised for specific applications.
Read more
Battery Chargers and Ingress Protection (IP) Ratings
Waterproof chargers are required for powering and charging electronic equipment in various industries, which operate in a wide range of different environments. Examples of some of these applications include marine, industrial, and emergency medical aid, allowing the charger or power supply and by extension the complete system to operate despite regular exposure to water, grime and dust.
Read more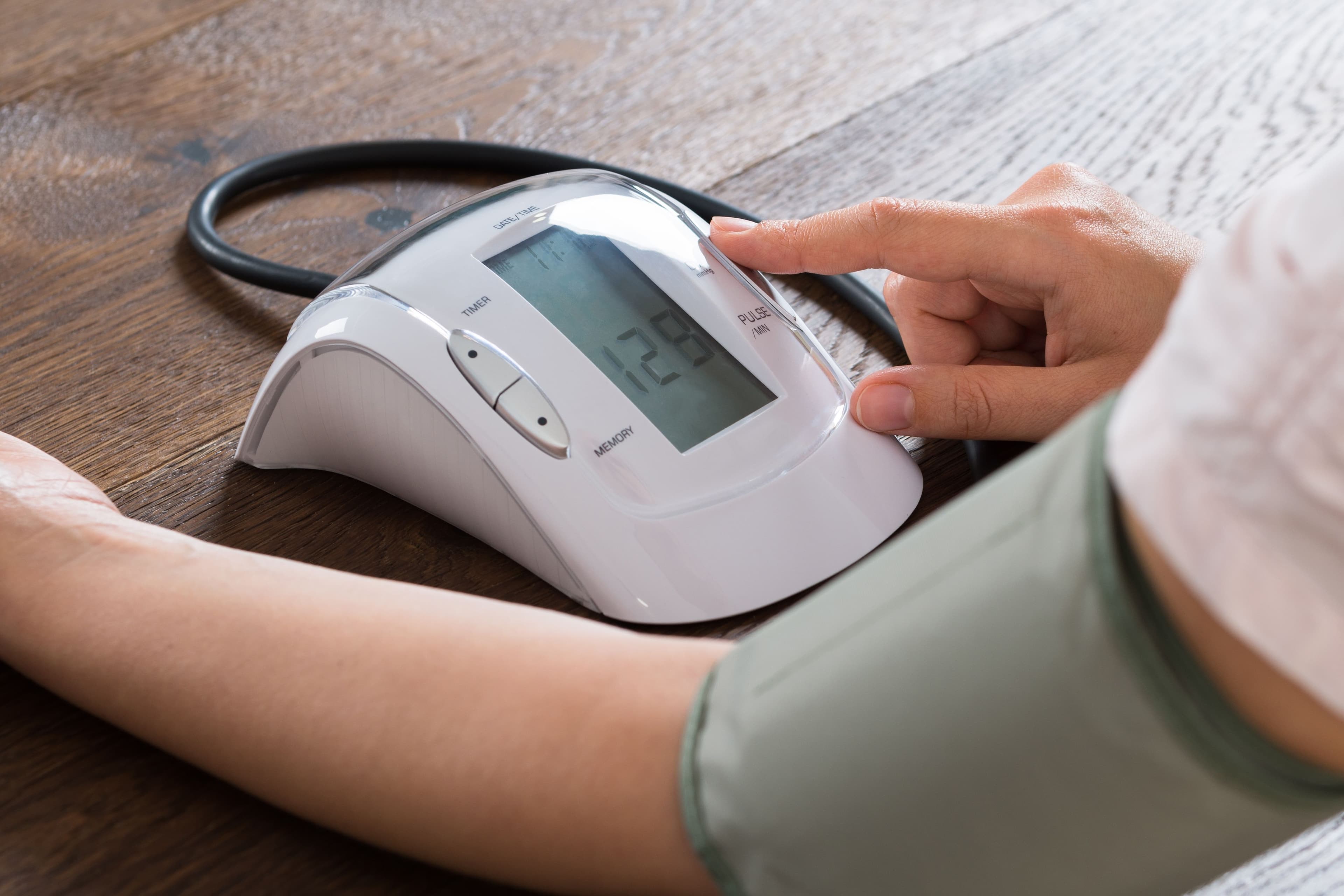
Home Healthcare & Medical Certification Basics
Medical certification ensures that electronic equipment meets stringent safety and performance standards. Medical systems must offer optimised, reliable performance, which in turn necessitates a high reliance on power.
Read more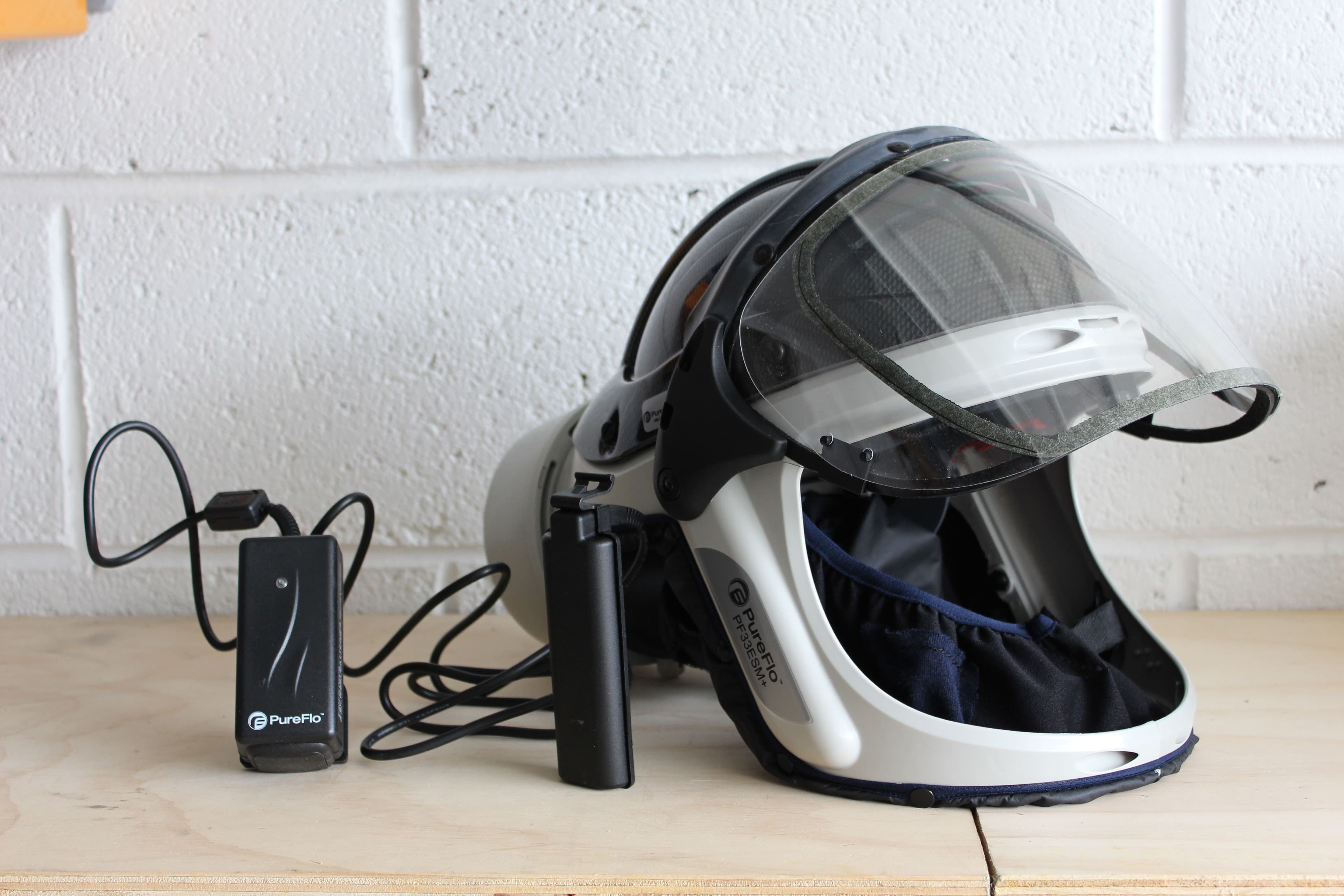
Application Story: GENTEX Corp
International power supply specialist Mascot has once again demonstrated the prowess of its manufacturing operation and global supply chain by delivering a rapid ramp-up in battery charger production to help one of its major global customers support the fight against the Covid-19 pandemic.
Read more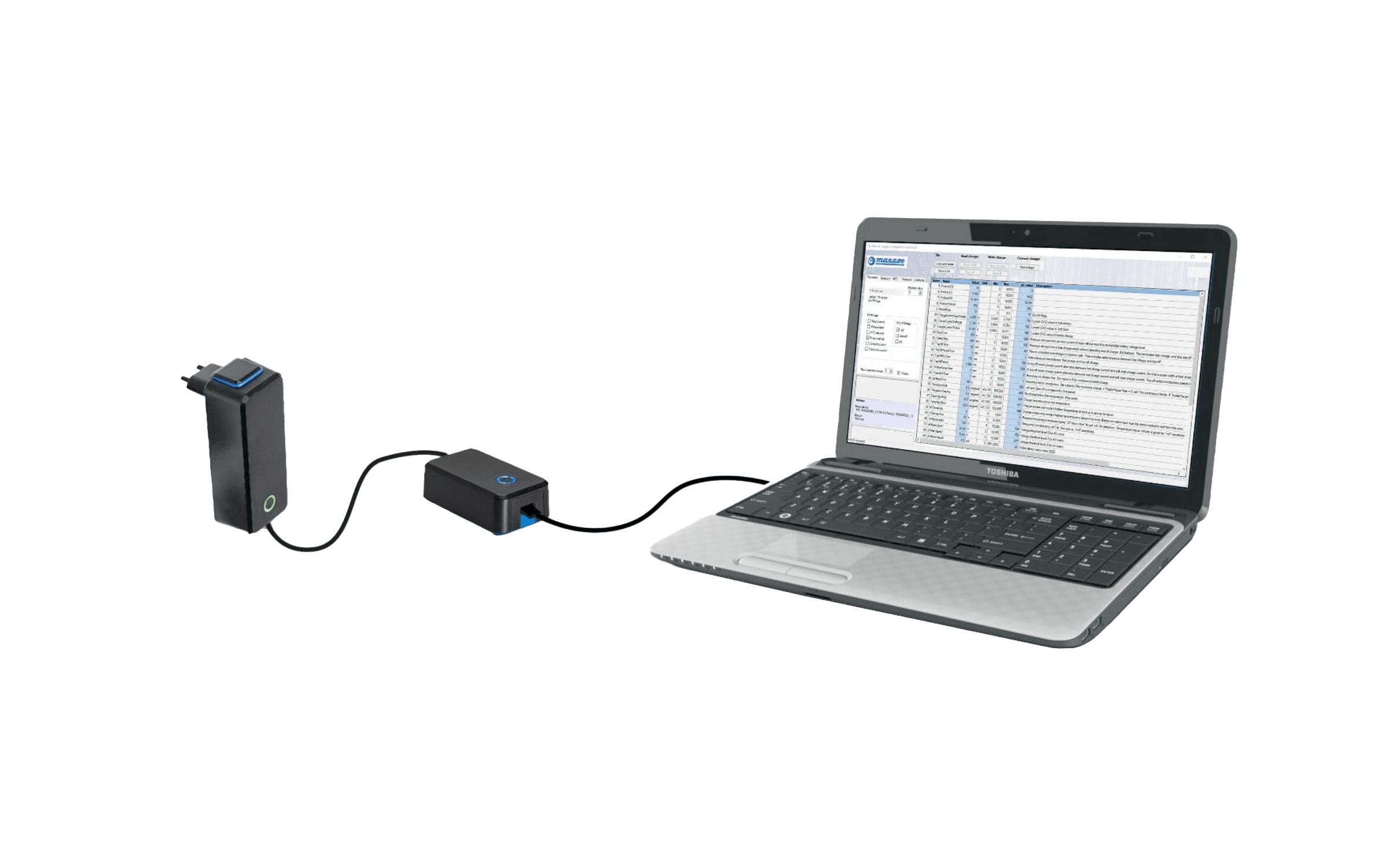
CBC (configurable battery charger) programming module for Lead Acid batteries
Configurable battery chargers offer users the flexibility to adjust charging parameters for increased optimisation and compatibility. Every Mascot CBC is ready for immediate use without the need for configuration. However, they can also be optimised for specific applications.
Read more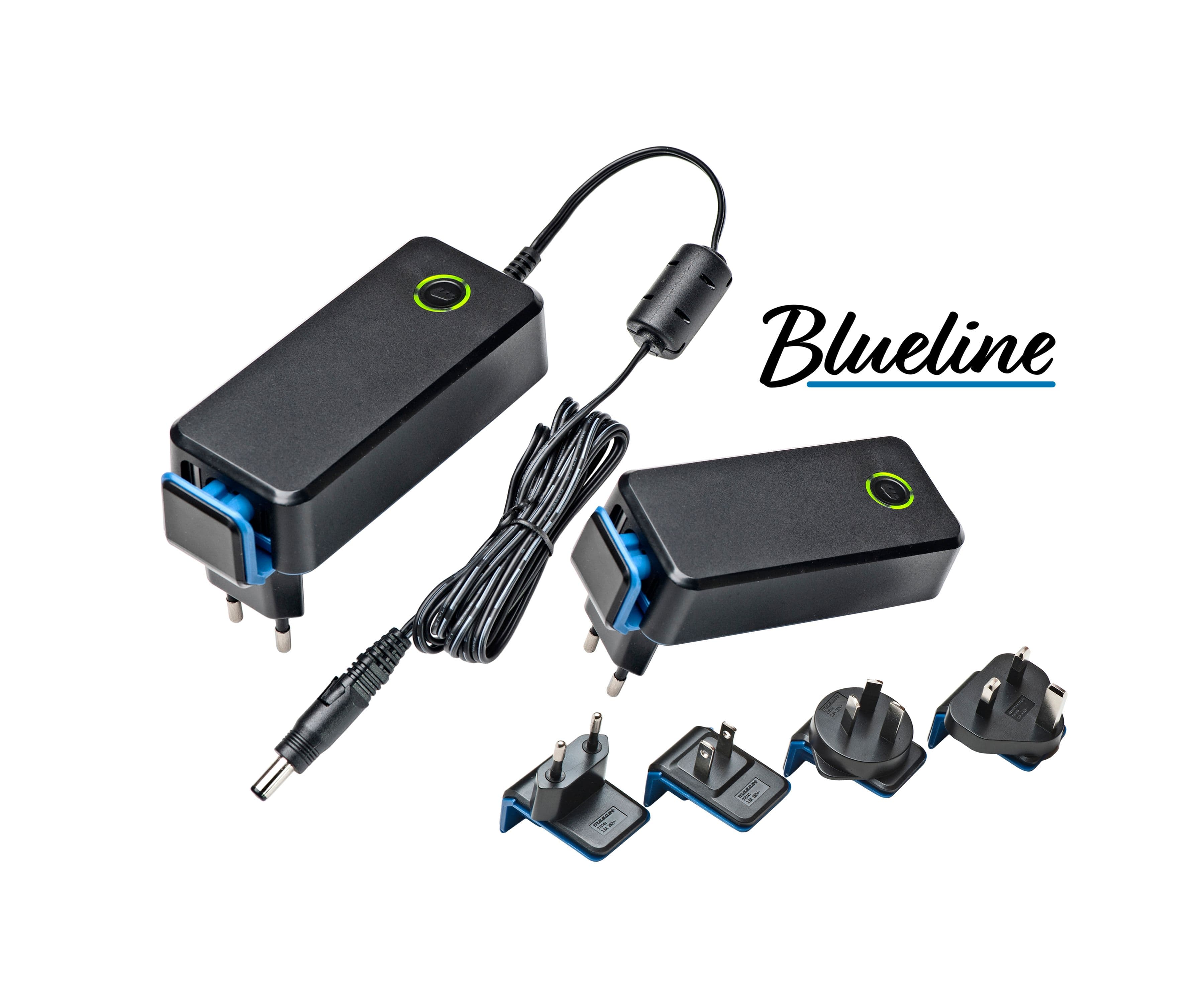
Mascot Blueline: An Eco-Friendly Power Solution
Eco-design focuses on creating products with minimal environmental impact throughout their life cycle. It involves considering environmental aspects in the product development, manufacture and end use. Examples of these include improving circularity and decreasing resistance leading to higher efficiencies and energy performance.
Read more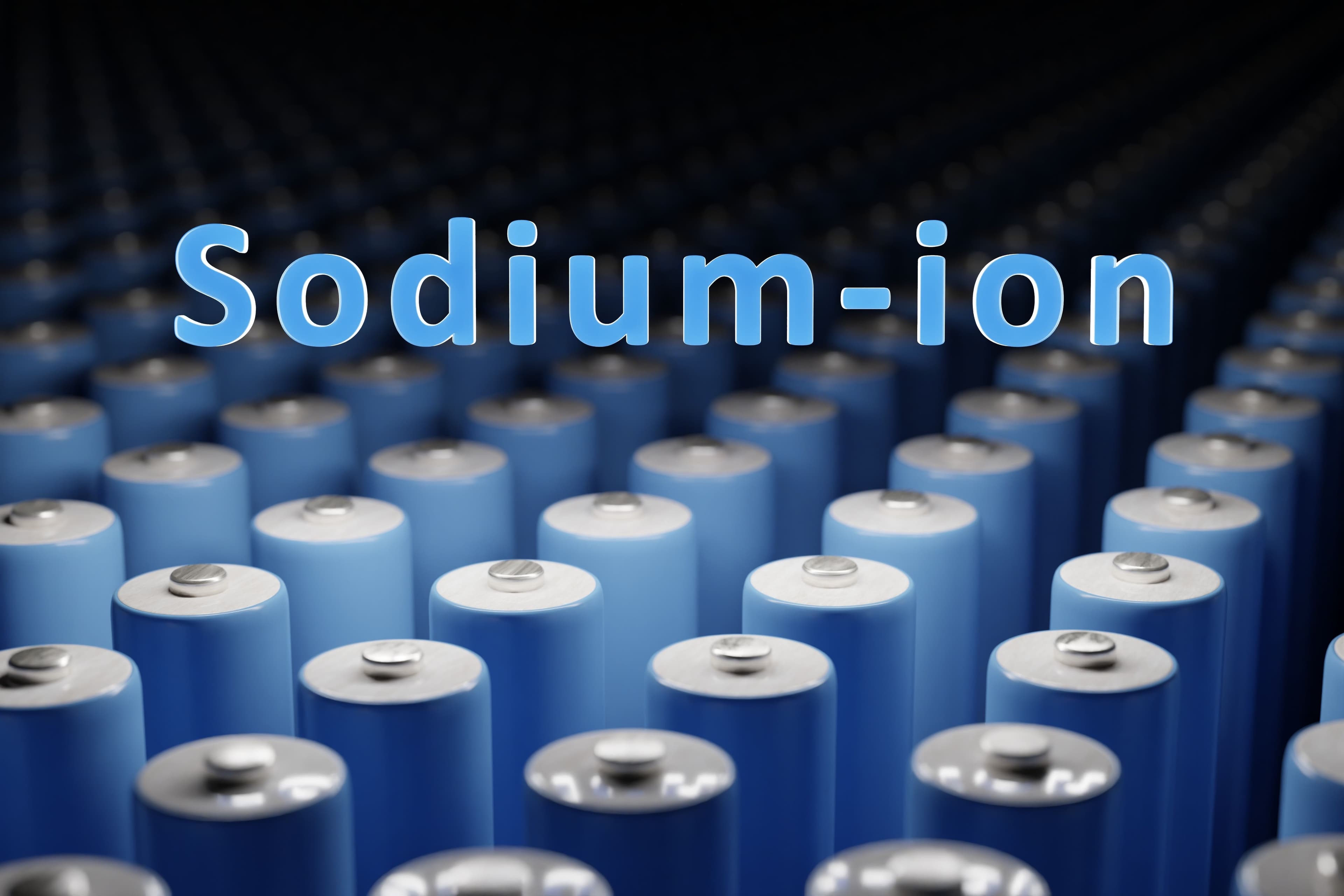
Sodium-Ion: a future-proofed battery solution
Lithium ion batteries have in the past few years become the preferred choice in a broad spectrum of applications. It’s easy to see why: they are versatile, boast high energy density and low self-discharge - below half of that of nickel-based batteries - and require little maintenance.
Read more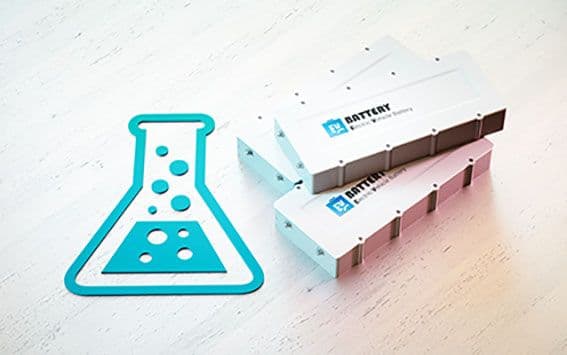
Getting the battery chemistry right
Most devices on the market now use rechargeable batteries. This creates a two-fold challenge for the engineer: addressing a string of battery chemistries in legacy products developed over a manufacturer’s lifetime, and the need to select the best available chemistry for a particular application.Understanding battery chemistry and testing and charging needs will ensure a product operates optimally and cost-effectively. Even a venerable and almost-vintage technology like lead acid is finding a new lease of life beyond the automobile in applications like microgrid storage.
Read more